Laying plywood to concrete floor is made in order to achieve the most smooth surface, because it is one of the conditions for high-quality laying of the floor covering. This material is quite easy to work, because It is easy to cut and fix on any base. In addition, plywood sheets have standard parameters, which greatly simplifies the procedure for calculating the required amount of raw materials.
Features of materials
The structure of plywood constitutes glued together fine wood sheets. As an adhesive composition for fastening such sheets, various resins are used. The minimum thickness of the plywood sheets is 6 mm. However, the most durable is plywood with a thickness of up to 12 mm. It is recommended that it is recommended to use in those construction work where material is required to be resistant to the effects of any loads.
Plywood on a concrete floor can be mounted exclusively on an even base. In the presence of drops or embossed, you need to perform a cement screed. The process of hardening such a screed lasts 1.5 months, and only on the expiration of this period of time can be performed any work. Before the direct laying of plywood, the screed should be coated with a layer of waterproofing.
Plywood on concrete floor photo:
In addition to performing a screed, before laying the phaneer to the concrete surface, it is necessary to determine the moisture content of the floor. This can be done in the following way:
- A small fragment of the polyethylene film should be put on the concrete surface, there will be one square meter.
- The edges of this film throughout the perimeter need to close to the base with the help of any items that will be at hand. The central part of the polyethylene remains free.
- It is necessary to wait 3 days, then look at the result. With a positive outcome, condensate will not be formed on the film. If he still appeared, in this case it is necessary to wait some time during which the screed will finally dry.
It is impossible to start working in the presence of condensate, since under these conditions, the plywood will quickly come into disrepair and rotates.
Varieties of plywood and the criteria for her choice
To make the right choice, you need to navigate in the varieties of plywood. The following types of this material are exist:
- FSF;
- FC;
- FOF.
They differ:
- resistance to moisture;
- material used to cover the upper layer;
- type of adhesive used.
In addition to these characteristics, plywood is divided into species depending on the raw materials used in the manufacture of raw materials. According to this criterion, birch and coniferous material are isolated.
- Plywood based on coniferous raw materials is not amenable to the process of rotting and fungal lesions. But due to the features of the composition, it is not recommended to use for interior decoration. As a rule, such material is used in roofing.
- For internal works, the most suitable is the plywood of the FC type, made of birch material. She, in turn, is divided into groups. Consider each other:
- the first group includes material having high quality indicators and the complete absence of any defects;
- the second group is represented by plywood, which may contain bitches and inserts in minor quantities;
- plywood on the concrete floor, the value of which is available for many consumers, has various kinds of defects - cracks and knots;
- the lowest quality indicators are the material relating to the last fourth group.
Based on these data, the most appropriate option will be the choice of birch plywood to the concrete floor, the price of which is fully justified by the quality. This is the material from the second group.
Plywood of the FC brand has an average moisture resistance.
To glue its layers, glue is used, which contains resin based on carbamides. These characteristics allow you to use this type of plywood for residential premises of any destination.
Plywood FSF is highly resistant to moisture, but due to the toxic composition of the adhesive, it is not suitable for use in residential premises.
How to choose a suitable glue for installation
To carry out the installation of sheets of plywood, the construction market today offers several types of adhesive composition.
- The safest environmental indicators have water-based glue. If it is applied as a retainer for sheets, you will need to use a dowel-nail. Such such glue sufficiently long time.
- Much quickly dries glue, having a solvent in its composition. Using it for mounting plywood, you can do without a dowel-nail. Such adhesive composition is much more convenient in use, but it has an unpleasant smell.
- Among all the varieties of glue, a two-component composition can be called the most convenient applied. For its drying, enough 24 hours. Also, when it does not need to be needed in additional fixation of the material. This is especially true if communications are in the concrete basis. Maintaining installation work through this glue can also be on a low screed. This option is possible if this glue is used together with epoxy primer.
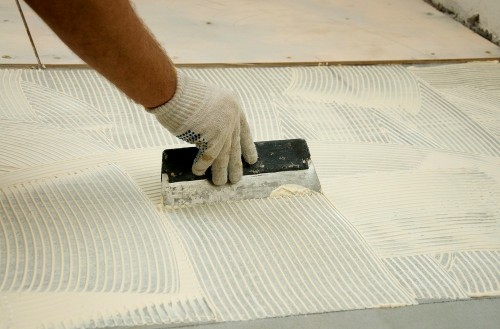
How to cut and adjust to Fan
- At the first stage of this process, the plywood sheets need to be cut into squares in size 60x60 cm each. The use of fragments of this size will give the opportunity to avoid voids, repeat uneven areas of the base, as well as obtain a greater number of seams.
- Before embarking on the layout of plywood sheets, you should make sure of their integrity. After that, sheets need to be decomposed on the floor and adjust their size under the location of the room. At the same time, the seam size should be taken into account: this indicator should be between the plywood fragments themselves from 8 mm to 1 cm; The distance between plywood and a wall can be up to 2 cm.
- In the process of laying sheets, it is necessary to make a slight offset so that all four seams do not cross at one point.
- The relevant numbers are put on the fitted sheets and are removed from the working base.
Preparatory Stage: Cleansing
From the surface of the working base, it is necessary to carefully remove all the contaminants, as well as the remains of old compositions - cement or paint. Irregularities need to be cleaned, and cracks to smell. The most suitable means for cleansing the surface of the floor is an industrial vacuum cleaner. But if it is not available, conventional remedies are quite suitable - broom or rag. Performing a cleansing procedure, it must be remembered that moisture should not be on the screed. In the opposite case, the quality of the sheets of plywood may suffer.
Application of the ground layer
For this stage, it is recommended to apply primer. This is the composition based on glue and a special solvent, which has several advantages over primer:
- The primer cleans the dust with high quality.
- Also, due to its ability to penetrate the structure of the floor surface, the top layer becomes more durable.
- In addition, the use of primer contributes to a better adhesion of various materials.
This composition is applied to the surface using a roller or brush.
Fastening plywood to concrete floor
- The first thing by means of a toothed spatula we apply to the working surface of the floor layer of the adhesive composition with a thickness of about 2 mm.
- Then we carry out the laying of sheets. Place sheets should be placed in accordance with their numbering.
- To exclude air flow sheets you need to roll the roller.
- After that, plywood sheets need to be secured by means of tapes with plastic dowels. The length of the self-samples for this purpose should be three times the thickness of the concrete base.
- Fixation points must be placed in the diagonal direction along the perimeter of the plywood fragment. The distance between them should be 20 cm. In the most concrete screed in those places where the mount is assumed, holes are made in advance. At the same time, the diameter of each such grooves must exceed the sizes of the screw of the self-press.
- Plastic dowels are inserted into these holes and screw screws.
Finishing Stage: Grinding
To get the most smooth base of plywood sheets, they need to be seized. This procedure is performed by grinding machine, which is treated with a parquet coating. An indicator of high-quality grinding is the complete absence on the surface of sowing or any irregularities.
After the workflow is completed, the quality of the laying should be checked.
- First you need to examine the surface - the sheets should not tightly lay down to the walls.
- Then, through the level, check whether the surface is quite smooth. When checking this criterion, deviation is allowed to 2 mm.
- Next, calculate the slope. This indicator should not exceed 50 mm.
- And last it should be verified in the absence of detachments. On the surface of the sheets you need to knock the hammer. The deaf sound will indicate the presence of a problem. In this case, the plywood sheet will need to be removed and reinstall.
Conclusion
Plywood is the most suitable material for aligning the concrete surface of the floor. Plywood sheets are easy to use and have certain advantages. And the process of their stacking implies several uncomplicated stages, to cope with which unprofessional will be able to successfully.
Methods of laying plywood and floor alignment is presented in video: